CENTRAL STERILE SUPPLY DEPARTMENT (CSSD)
CSSD stands for Central Sterile Services Department, also known as Sterile Processing Department (SPD) or Central Sterile Supply Department. This is a crucial department within healthcare facilities, responsible for the sterilization, processing, storage, and distribution of medical and surgical instruments and equipment. The primary goal of the CSSD is to ensure that medical instruments are properly cleaned, sterilized, and maintained to prevent the spread of infections.
Functions of CSSD
- Sterile processing departments are typically divided into four major areas to accomplish the functions of decontamination, assembly and sterile processing, sterile storage, and distribution
- In the decontamination area, reusable equipment, instruments, and supplies are cleaned and decontaminated by means of manual or mechanical cleaning processes and chemical disinfection
- Clean items are received in the assembly and packaging area from the decontamination area and are then assembled and prepared for issue, storage, or further processing (like sterilization)
- After assembly or sterilization, items are transferred to the sterile storage area until it’s time for them to be issued
- Several major functions are carried out in the distribution area: case cart preparation and delivery; exchange cart inventory; replenishment and delivery; telephone-order and requisition-order filling; and sometimes, patient care equipment delivery
Importance of CSSD:
- Infection Control:
- Proper sterilization and processing of instruments in the CSSD are critical for preventing healthcare-associated infections (HAIs).
- Patient Safety:
- Sterile instruments are essential for surgical procedures and various medical interventions, ensuring patient safety and reducing the risk of postoperative complications.
- Regulatory Compliance:
- CSSD must adhere to regulatory guidelines and standards set by health authorities to ensure the quality and safety of sterilization processes.
- Efficiency in Healthcare Delivery:
- A well-functioning CSSD contributes to the efficient delivery of healthcare services by providing healthcare units with sterile instruments in a timely manner.
- Cost-effectiveness:
- Proper maintenance and reprocessing of reusable instruments in the CSSD can be cost-effective compared to the continuous purchase of disposable instruments.
CSSD Work Flow in Hospital
Unsterile things — collection area — packaging area — process area — sterile area — collection area
The workflow in a Central Sterile Services Department (CSSD) involves a series of systematic steps to ensure the proper cleaning, decontamination, sterilization, and distribution of medical instruments and equipment. The workflow may vary slightly among different healthcare facilities, but here is a general overview of the typical CSSD workflow:
1. Receiving and Sorting:
- Incoming Instruments: Receive used instruments and equipment from various healthcare units.
- Sorting: Sort instruments based on type, material, and contamination level.
2. Cleaning and Decontamination:
- Pre-Cleaning: Remove gross debris and organic materials from instruments.
- Cleaning: Use mechanical or automated cleaning equipment to thoroughly clean instruments.
- Decontamination: Employ disinfectants or detergent solutions to eliminate remaining microorganisms.
3. Assembly and Packaging:
- Sorting and Inspection: Sort cleaned instruments and inspect them for damage or wear.
- Assembly: Assemble instrument sets according to standard protocols.
- Packaging: Package instruments in materials suitable for sterilization, ensuring proper labeling and documentation.
4. Sterilization:
- Method Selection: Choose an appropriate sterilization method based on the type of instruments.
- Load Preparation: Arrange packaged instruments in sterilization trays or containers.
- Sterilization Process: Perform sterilization using methods such as autoclaving (steam sterilization), ethylene oxide (ETO), or other approved methods.
- Monitoring: Monitor sterilization processes with chemical and biological indicators.
5. Quality Control:
- Inspection: Inspect sterilized instruments for signs of damage or inadequate sterilization.
- Testing: Conduct periodic testing of sterilization equipment and perform routine checks on instruments.
- Record Keeping: Maintain detailed records of sterilization processes, including load contents, dates, and results of monitoring.
6. Storage:
- Storage Conditions: Store sterilized instruments in designated areas under controlled environmental conditions.
- Inventory Management: Monitor inventory levels, ensuring an adequate supply of sterile instruments for various departments.
7. Distribution:
- Order Processing: Receive requests for sterile instruments from healthcare units.
- Packing and Transport: Pack requested instruments and distribute them to the appropriate departments.
- Documentation: Maintain accurate documentation of distributed instruments.
8. Education and Training:
- Staff Training: Provide ongoing education and training for CSSD staff on proper procedures, infection control, and equipment use.
- Communication: Collaborate with healthcare units to provide information on proper handling and care of instruments.
9. Continuous Improvement:
- Performance Evaluation: Regularly evaluate the performance of the CSSD, including efficiency, quality, and compliance with standards.
- Feedback Mechanism: Establish a feedback mechanism for continuous improvement based on staff input, audits, and regulatory updates.
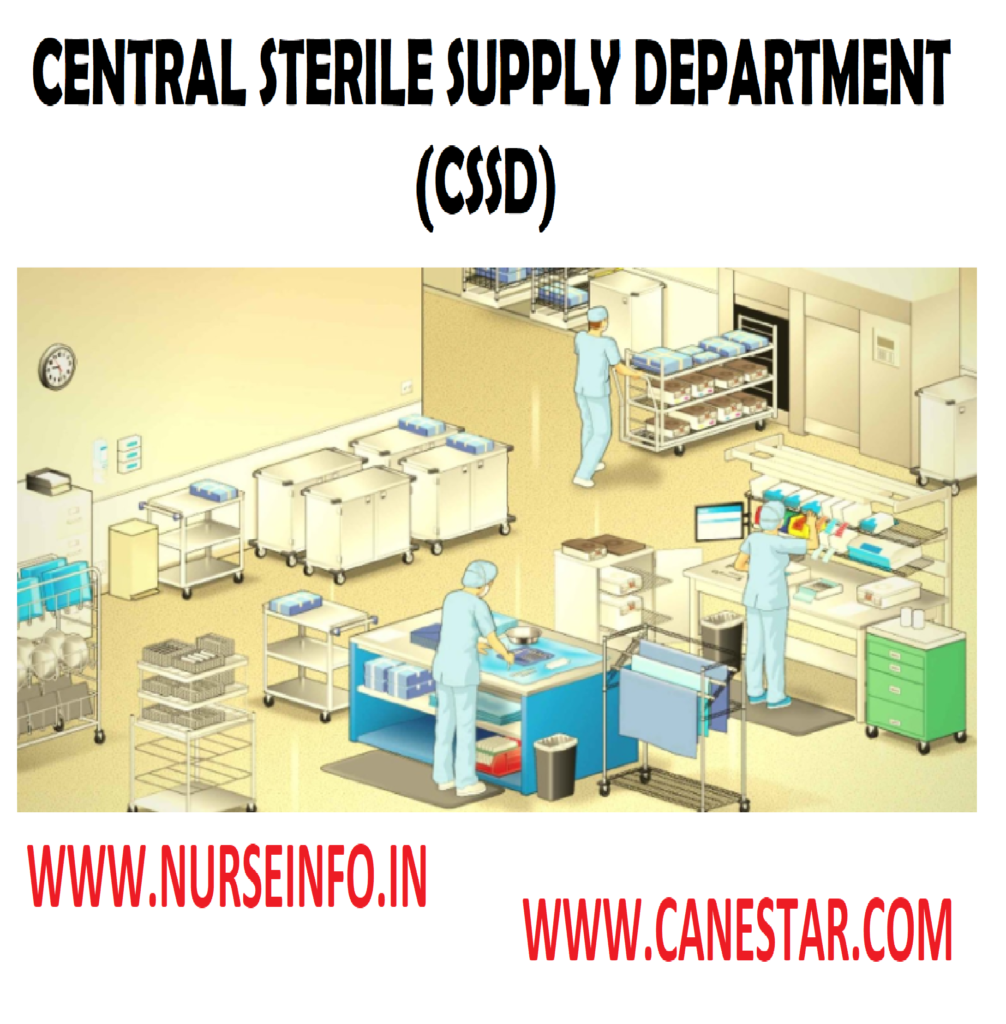